Features and Applications of Tower-Type Tungsten Carbide Alloy Tooth Water Well Drill Bits
Jul 25,2025
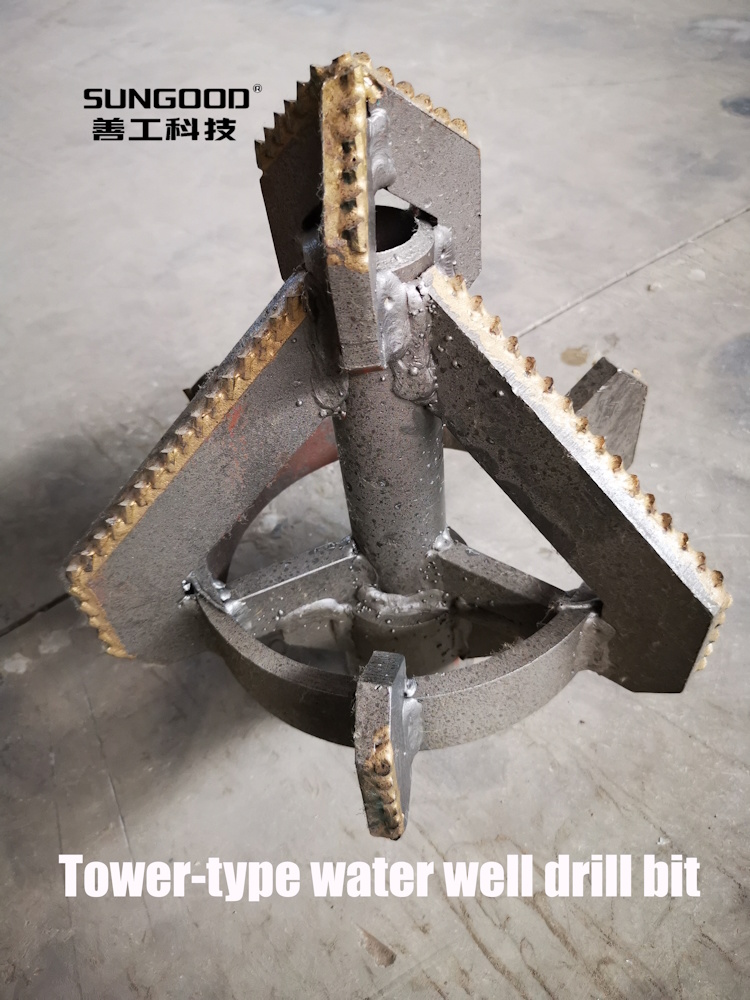
I. Core Features
- Material Characteristics: Tungsten Carbide Alloy Teeth (Hard Alloy)
- Composition & Hardness: Main components are Tungsten Carbide (WC) and Cobalt (Co), accounting for 99%. Hardness is 3 times that of ordinary steel; red hardness reaches 800–1000°C. Exceptional wear resistance, suitable for prolonged high-speed drilling.
- Impact Resistance Shortcoming: Brittle, low bending strength. Requires proper drilling pressure (light pressure, high speed) to prevent tooth breakage.
- Efficiency Advantage: Cutting speed is 4–7 times that of high-speed steel bits, significantly improving drilling efficiency.
- Composition & Hardness: Main components are Tungsten Carbide (WC) and Cobalt (Co), accounting for 99%. Hardness is 3 times that of ordinary steel; red hardness reaches 800–1000°C. Exceptional wear resistance, suitable for prolonged high-speed drilling.
- Structural Design: Tower-Type Multi-Layer Layout
- Stepped Alloy Tooth Arrangement: The bit uses multi-layer annularly distributed alloy teeth, forming a "tower-type" contour. Outer teeth are responsible for hole reaming and wall trimming; central teeth focus on breaking the rock core, achieving efficient chip removal and wellbore stability.
- Cooling & Chip Removal Optimization: The tower structure provides coolant channels and flutes to ensure timely removal of cuttings and bit cooling, preventing high-temperature-induced passivation.
- Stepped Alloy Tooth Arrangement: The bit uses multi-layer annularly distributed alloy teeth, forming a "tower-type" contour. Outer teeth are responsible for hole reaming and wall trimming; central teeth focus on breaking the rock core, achieving efficient chip removal and wellbore stability.
- Performance Advantages
- Long Service Life: Excellent wear resistance of tungsten carbide alloy teeth. Life is 5–6 times longer than conventional bits in abrasive formations (e.g., granite, quartz sandstone).
- High Precision Hole: The tower structure provides self-centering capability, ensuring high hole verticality and smooth wellbore walls, reducing subsequent well repair needs.
- Cuttings Control: Produces coarse-grained cuttings, reducing dust pollution and improving the work environment.
- Long Service Life: Excellent wear resistance of tungsten carbide alloy teeth. Life is 5–6 times longer than conventional bits in abrasive formations (e.g., granite, quartz sandstone).
II. Typical Application Scenarios
- Hydrological and Agricultural Water Well Drilling
Suitable for medium-hard to hard formations (e.g., basalt, limestone), depths exceeding 100 meters. Tower structure ensures borehole verticality; alloy teeth efficiently break rock; cooling system handles prolonged continuous operation. - Mining and Engineering Geological Exploration
Excellent performance in complex formations like gravel layers and fracture zones: Multi-layer alloy teeth break large particles stepwise, reducing bit jamming risk; wear resistance adapts to highly abrasive formations. - Geothermal Wells and Foundation Pile Hole Construction
Geothermal wells require drilling through high-temperature rock layers. WC-Co's high-temperature resistance (>800°C) ensures stability. In pile foundation engineering, tower bits enable single-pass drilling of large-diameter (>300mm) deep holes. - Complex Formation Adaptability
Performance comparison in different formations:
Formation Type | Performance |
---|---|
Soft Soil | Efficient cutting, but requires controlled speed to prevent bit balling. |
Sand & Gravel Layer | Tower structure crushes gravel stepwise; smooth cuttings removal. |
Bedrock (Granite etc.) | Significant advantage of wear-resistant alloy teeth; lifespan extends over 3 times. |
Highly Fractured Formation | Strong resistance to radial wear, reducing hole deviation risk. |
⚠️ III. Operation and Maintenance Points
- Parameter Matching
- Rotation Speed: Recommended speed: 30m/min linear velocity (e.g., for Ø100mm bit, speed ≈95rpm).
- Weight on Bit (WOB): Start with light pressure (apply pressure after cutting in 1–2mm) to avoid impact loads causing tooth breakage.
- Rotation Speed: Recommended speed: 30m/min linear velocity (e.g., for Ø100mm bit, speed ≈95rpm).
- Cooling and Lubrication
- Internal cooling system MUST be used. Coolant flow rate ≥20L/min to prevent high-temperature sintering of the matrix.
- Mud sand content should be <1% to minimize unnecessary wear.
- Internal cooling system MUST be used. Coolant flow rate ≥20L/min to prevent high-temperature sintering of the matrix.
- Sharpening and Repair
- After blunting, requires sharpening with a dedicated 5-axis grinding machine to restore cutting angles (typically 140°) and stepped height differences.
- Avoid manual sharpening causing geometric accuracy imbalance.
- After blunting, requires sharpening with a dedicated 5-axis grinding machine to restore cutting angles (typically 140°) and stepped height differences.
💎 IV. Technology Evolution Direction
- Coating Technology: Coatings like TiAlN can further increase surface hardness (>3500HV), extending life by 30%.
- Modular Design: Replaceable alloy tooth units, reducing overall replacement costs.
Conclusion
SUNGOOD TECH's Tower-Type Tungsten Carbide Alloy Tooth water well drill bits, with wear-resistant alloy + stepped structure at their core, are an efficient solution for deep well and hard rock drilling. Their value is fully realized in efficient hole formation in complex formations, low maintenance costs, and long service life—especially suitable for hydrological exploration, mining engineering, and similar applications. Future developments in coatings and modular design will further expand their application boundaries.
PREVIOUS:
Contact Us