PDC Stepped Drill Bits: Efficient Drilling for Water Wells and Mining
Jul 28,2025
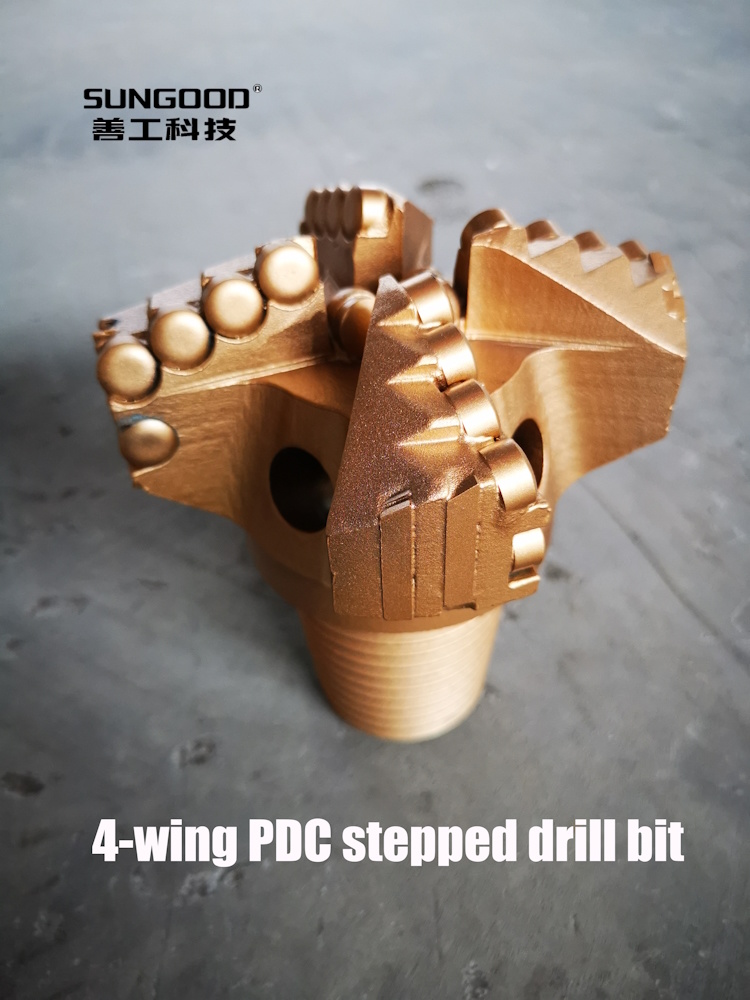
Structural Design Features
- Stepped Cutting Layout
- Zoned Design: The crown is divided into inner cone, nose, shoulder, taper, and gage sections. Inner cones centralize positioning for initial rock fragmentation, while outer sections expand the bore diameter.
- Dry Chip Removal: Spiral or radial flutes (e.g., constant cross-section designs) efficiently eject debris without hydraulic nozzles.
- Zoned Design: The crown is divided into inner cone, nose, shoulder, taper, and gage sections. Inner cones centralize positioning for initial rock fragmentation, while outer sections expand the bore diameter.
- Multi-Blade & Hybrid Cutters
- Primary/Secondary Blades: Main blades perform core fragmentation; secondary conical PDC teeth reduce vibration. Asymmetric layouts enhance directional stability (±0.5° precision).
- Special-Shaped Cutters: Conical/chisel-shaped PDC teeth improve penetration in medium-hard strata.
- Primary/Secondary Blades: Main blades perform core fragmentation; secondary conical PDC teeth reduce vibration. Asymmetric layouts enhance directional stability (±0.5° precision).
- Material-Specific Adaptations
- Soft Formations (clay, gypsum): Low-angle steps (15–25°) prevent sediment buildup.
- Hard Formations (granite, quartzite): High-angle tiers (45–60°) maximize point loading.
- Soft Formations (clay, gypsum): Low-angle steps (15–25°) prevent sediment buildup.
Material and Manufacturing
- Advanced PDC Materials
- Wear Resistance: 4–5mm diamond layers increase durability by 300%, suitable for abrasive quartzite or concrete.
- Gage Protection: Thermally stable diamond (TSP) or diamond-impregnated blocks reinforce gage sections.
- Wear Resistance: 4–5mm diamond layers increase durability by 300%, suitable for abrasive quartzite or concrete.
- Precision Production
- 3D-Printed Bodies: Metal additive manufacturing ensures ±0.1mm tier alignment (e.g., SUNGOOD TECH’s 72-hour rapid prototyping).
- Welding Technology: Induction-oxygen welding secures PDC to tungsten carbide bases.
- 3D-Printed Bodies: Metal additive manufacturing ensures ±0.1mm tier alignment (e.g., SUNGOOD TECH’s 72-hour rapid prototyping).
Applications
- Water Wells: Drills 200–500m crystalline rock sections in single runs. SUNGOOD TECH-supported Kenyan projects achieved 400m granite wells with <0.5° deviation.
- Construction: Rapid core drilling in concrete/stone piles (diameter: 100–500mm).
- Mining: Efficient penetration in iron/gold ores (≤8 Mohs hardness).
Limitations & Solutions
- Abrasive Strata: Lifespan drops 60% in quartz-rich formations.
→ SUNGOOD TECH integrates TSP blocks to extend service life. - Dry-Drilling Heat: Overheating risk beyond 40m depth.
→ Ceramic heat-dissipation grooves mitigate temperature.
Design Specifications by Application
Application | Cutter Design | Flute System |
---|---|---|
Water Well (Soft Rock) | 16–19mm PDC | Wide spiral flutes |
Concrete Piling | Impact-resistant tips | Shallow stepped flutes |
Metal Mining | Micro-stepped TSP teeth | Reinforced radial flow |
Conclusion
PDC stepped drill bits enable efficient, precise drilling in non-oil sectors through robust stepped geometry and diamond-enhanced durability. SUNGOOD TECH drives innovations in dry-operation stability and rapid manufacturing, setting benchmarks for complex geology.
🔗 Discover precision engineering for demanding terrains: SUNGOOD TECH Professional Drilling Solutions
PREVIOUS:
Contact Us