Drill Bit Cutters: Tungsten Carbide or PDC?
Jul 02,2025
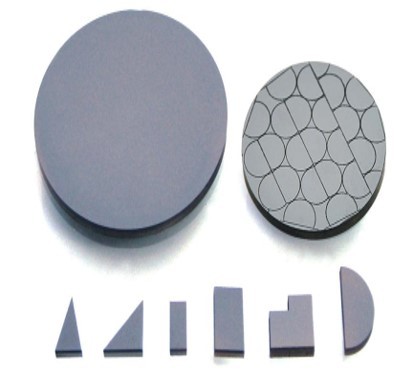
Formation Complexity Dictates Cutter Choice
In oil drilling and mining, tungsten carbide cutters and PDC cutters serve as critical "teeth" with distinct advantages:
- Tungsten carbide cutters act as "shock absorbers": WC-Co structure delivers exceptional toughness, excelling in gravel zones and fractured formations, though less efficient in soft rock.
- PDC cutters perform as "precision blades": Diamond table + carbide substrate enables extreme abrasion resistance, boosting ROP in homogeneous shale/sandstone, yet vulnerable to hard interbeds.
Hybrid Innovation Solves Application Challenges
As directional drilling and deep exploration advance, standalone cutter selection fails in complex geology. Cutting-edge solutions integrate both via 3D cutter placement technology:
- PDC cutters drive ROP as primary cutting units
- Tungsten carbide cutters shield bit shoulders/gauge areas as "armor"
- Backup carbide teeth embedded in crown tackle sudden hard streaks
Field test in shale gas project: Hybrid bits achieved 230% longer lifespan than pure PDC bits in flint-interbedded formations with only 7% ROP reduction.
SUNGOOD TECH’s Rock-Breaking Philosophy
With decade-long expertise, SUNGOOD TECH pioneers the "Dynamic Cutter Ratio" system:
- AI geological modeling predicts formation transition curves
- Dynamic tungsten carbide/PDC ratio configuration across bit quadrants
- Patented stepped hybrid sockets dissipate thermal stress
The SD-Series hybrid bits set a 1,389-meter single-run record in Ordos Basin conglomerate, increasing ROP by 30% versus conventional solutions.
#IndustryInsight
[Drill Bit Evolution: From Steel Teeth to Smart Hybrid Cutters]
→ Discover how SUNGOOD TECH’s hybrid cutter technology redefines deep exploration rules
Explore Advanced Solutions
Contact Us